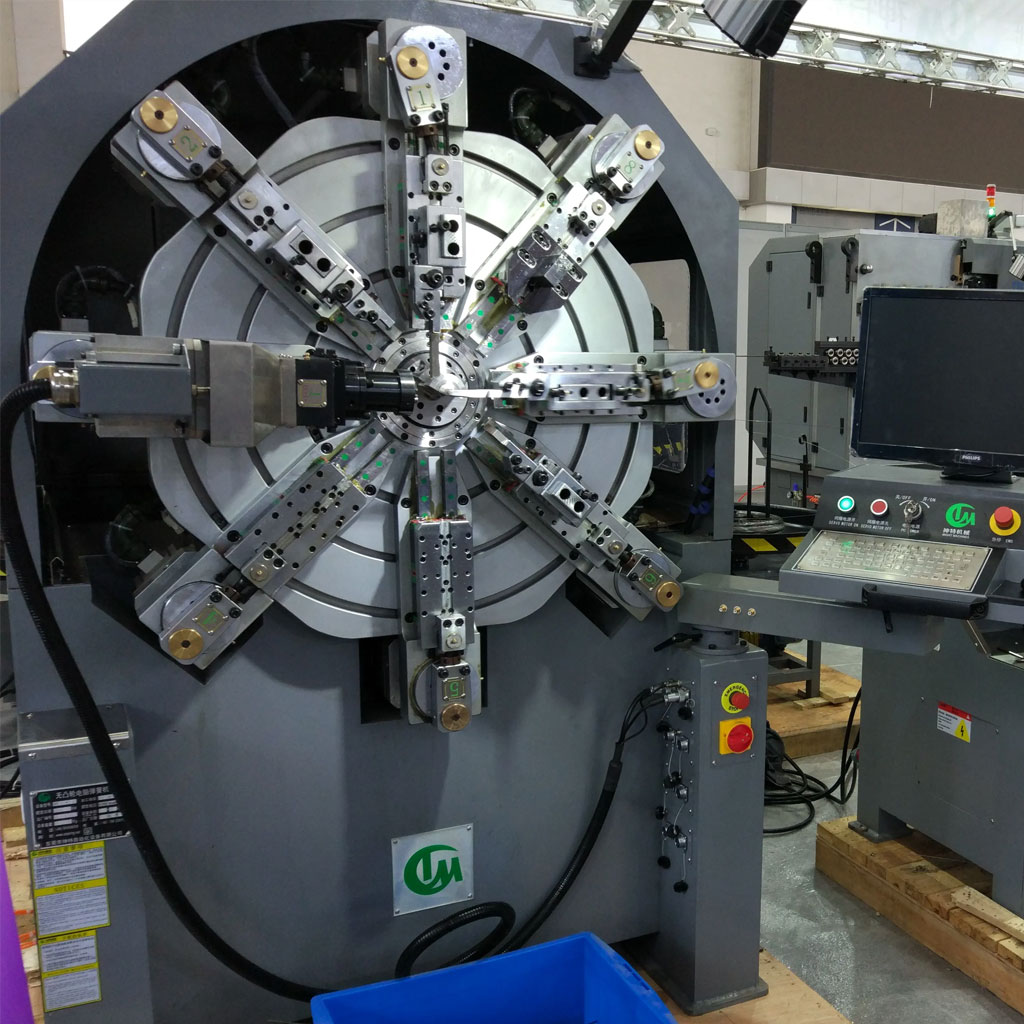
Spring Machining
Spring is a device that changes its shape under the action of an external force to generate energy. Usually, the change in shape is directly related to the magnitude of the applied force. However, if a large force is applied, the spring will be permanently deformed and will not return to its original shape.
The modern precision spring machine has improved the high efficiency and precision of the production and machining of the spring: in the industrialized production industry, the precision of the spring products is very high. Servo control system and industrial electrical components have greatly ensured the high efficiency and reliability of the spring machine operation. At the same time, high-precision transmission gears, imported bearings and prefabricated components of high-depth springs machining machinery and equipment can better ensure the precision requirements of production and mass machining, and can also develop the diameter of the product anytime and anywhere according to the working conditions on the display screen.
Reduce the adjustment difficulty and actual operation requirements of the machine and equipment: the spring machine has a Chinese system operation panel, the page is easy to use, and the machine and equipment can be accurately operated. According to the individual AC servo motors of the upper control system, all motors can be controlled to operate simultaneously or independently. The design concept of automatic shutdown and the automatic acceleration function of the wire rack when disconnecting or winding the wire greatly reduces the adjustment difficulty of the spring machine. Factors and practical regulations!
On the other hand, the quality of the spring machine is relatively light for the product of the spring machine, and there are quality advantages in the whole process of manufacturing the spring yellow. When the spring yellow is produced and processed, it is usually all relatively For those who pay attention to details and problems, when the quality requirements are relatively high, the machinery and equipment should not be too heavy, otherwise it will harm the actual effect of production, so the spring machine must be relatively light, so that the produced springs have advantages!
For the shape design of springs, many people have developed various mathematical equations to describe the characteristics of the spring, based on factors such as wire composition and size, coil diameter, number of coils, and the amount of expected external force. These equations have been incorporated into computer software to simplify the design process.
Two Metal Forming Processes Of Springs
The spring machine is a device that realizes the automation of spring processing. Hot forming and cold forming are the two main processes of spring processing at present. Faced with these two processes, the situation of the spring machine is different. The following is a brief introduction to the two forming processes of spring processing!
The Cold Forming Process Of Metal Springs
The one-time automation capability of the cold forming process, the cold forming spring machine has been developed to 12 claws, and the steel wire in the range of (0.3~14) mm is basically formed at one time by the 8 claws forming machine, and the maximum size of the process range can reach 20mm, 2000mpa , the rotation ratio is 5, but the cold forming process of Minic-Block spring and eccentric spring of variable diameter or equal diameter material still has limitations. The current development direction of forming process equipment:
- Improve the forming speed, the main development trend is to improve the forming speed of the equipment, that is, the production efficiency;
- Improve the accuracy of equipment parts, enhance the heat treatment effect, and improve the durability of the equipment;
- Add a length sensor and a laser rangefinder to automatically control the manufacturing process of the CNC molding machine;
The Thermoforming Process Of Metal Springs
- The speed capability of the thermoforming process. At present, there is only a CNC 2-axis hot coil spring machine on the specification (9~25) mm in my country, and the maximum speed is 17 pieces per minute. Compared with the spring machines in developed countries, there is a big gap.
- The control ability of large-scale spring thermoforming process. Since there is only a CNC 2-axis hot-rolled spring machine, the shape control is less in three directions, and the precision is poor; there is no automatic bar rotation control and adjustment mechanism, so the forming process level and ability of the hot-rolled spring are low. Therefore, the precision level of the spring and the level of surface oxidation decarburization are also lower. These are some of the problems existing in the hot forming process of domestic spring machines.
The Production Process Of Metal Spring
Spring Manufacturing has cold rolling, hot rolling and other cnc machining methods, and then it has to go through a series of machining such as grinding, shot peening, heat treatment, setting, coating, packaging and other processes. Let us briefly introduce the complete process of the lower spring.
- Helical tension spring: rolling, stress relief annealing, hook and loop production, (cut tail), stress relief annealing, standing treatment, inspection, surface anti-corrosion treatment, packaging.
- Helical torsion spring: rolling, stress relief annealing, torsion arm fabrication, tail trimming, stress relief annealing, standing treatment, inspection, surface anti-corrosion treatment, packaging.
The manufacturing processes of the helical tension and torsion springs described above are all wound on a common coil spring machine and then process the shackles or torsion arms at both ends. In recent years, many manufacturers at home and abroad have produced and used computerized forming machines or special forming machines. The shape of the spring body and tail can be completed on the forming machine at one time, eliminating the need for springs machining hooks and rings or torsion arms.
When using materials that need to be quenched and tempered after forming, the main difference from the above process is that quenching and tempering are required after forming, and sometimes the spring end springs machining needs to be normalized.
The process with brackets is a non-fixed process, and whether it is carried out depends on the performance requirements of the spring.