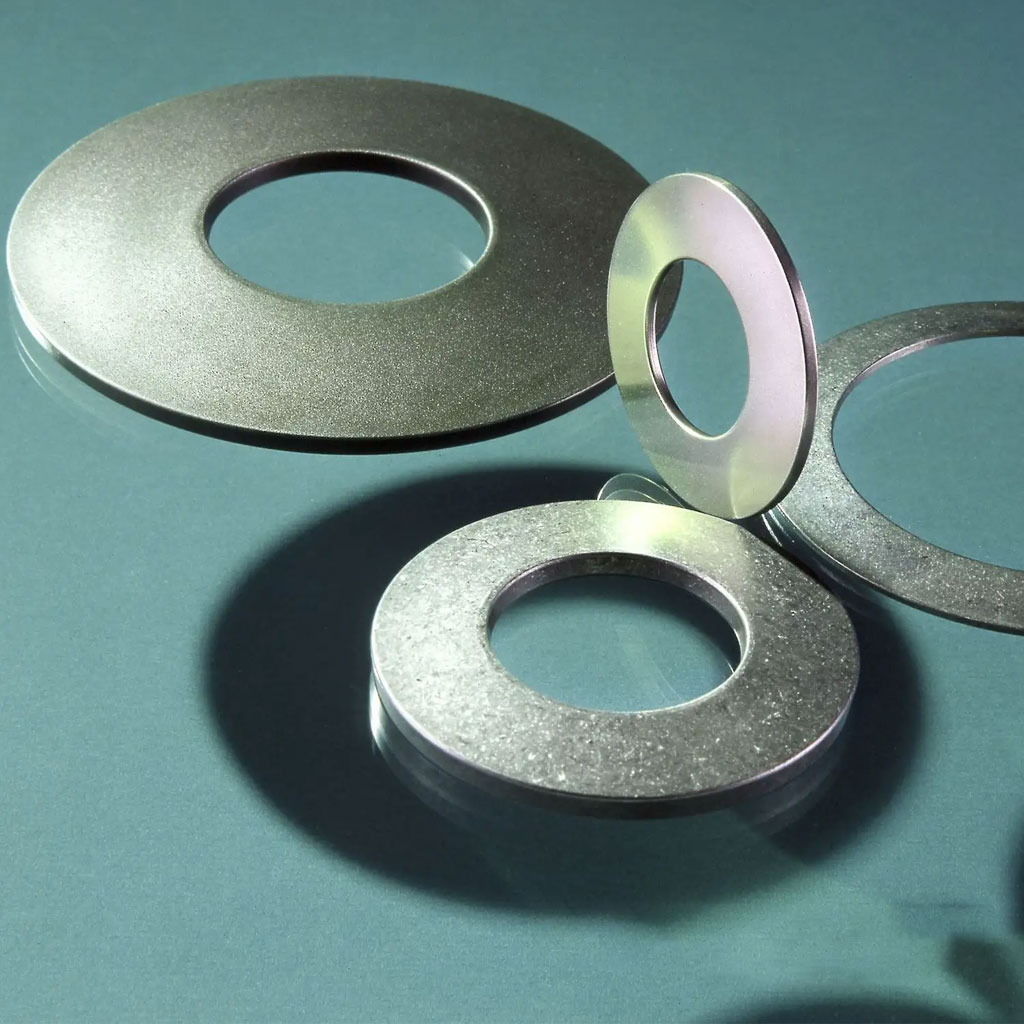
Disc Springs
It is a kind of mechanical fittings with a shape resembling a ring gasket, but with different materials—special springs. Because of its shape like a bowl, it is called a disc spring.
Generally speaking, it works by providing enough elastic stretch through a considerable amount of stacking.
Due to the characteristics of variable stiffness and compact installation, it is widely used in machinery and equipment industry, petroleum industry, automobile industry, aerospace industry and other fields. Largely replaced the cylindrical coil spring.
Disc springs are designed for short strokes and high elastic force, and their typical applications are to generate large elastic force in a small space, such as: bolt tightening, rail transit, die stamping, packaging machinery, power transmission and transformation devices, etc.
Disc springs, referred to as disc springs (DIN2093), are also mistakenly written as butterfly springs. In the mid-19th century, disc springs were invented and used. At that time, Belleville, a Frenchman, applied for a design patent for disc springs. Today, disc springs are still called Belleville Springs in some places.
In the 21st century, disc springs are used in more fields, such as aerospace, defense systems, medical equipment, automobiles, electric power, construction, machine tools and other industries…
The universal standard for disc springs in the world is the German DIN2093 standard. The disc spring standard used in my country earlier was GB/T1972-1992. Now the national standard for disc springs implemented in my country is GB/T1972-2005.
A truncated conical sheet spring stamped from metal strip, sheet or forged blank, its load and deformation have a nonlinear relationship. Generally divided into ordinary butterfly springs, butterfly springs with radial grooves, and trapezoidal section butterfly springs. Because the deformation and load value of the single-piece butterfly spring often cannot meet the requirements. So it is generally used in combination. The butterfly spring has small deformation and high load capacity, saves space, and can obtain ideal loading characteristics through different combinations.
The disc spring is in the shape of a conical disc. As a sealing aid, it can be used alone or in series or in parallel. The upper inner edge and the lower outer edge are subjected to static or dynamic loads acting in the axial direction and are compressed. It is then deformed until it is flattened, and is used as a live load in the form of stored energy. When necessary, it is automatically converted into an additional compressive load required by the seal to reduce the continuous requirements for tightening in the use of gaskets and packings. Reduce unnecessary Downtime for repairs and leakage losses.
Custom Disc Springs Manufacturer In China
If you need high spring force and short travel, disc springs will be your best choice.
Disc springs can be stacked to obtain different combinations of strokes and elastic forces; even if the thickness of the disc springs is different, they can also be stacked. The superimposed form of disc springs can be divided into three categories:
- Overlap: two identical disc springs are superimposed relative to each other, the stroke is doubled and the stiffness is halved;
- Parallel stacking: two identical disc springs are stacked in sequence, the stroke remains unchanged and the stiffness is doubled;
- Composite stacking: Multiple disc springs are combined in two ways: stacking and cumming at the same time, resulting in a variety of mechanical effects.
A plurality of disc springs are combined in two ways of stacking and stacking at the same time, resulting in a variety of mechanical effects.
The Case Studies Of Disc Springs
Currently, our non-standard disc springs are exported to America, Canada, Australia, United Kingdom, Germany, France, Sout Africa, and many other countries all over the world. We are ISO9001-2015 registered and also certified by SGS.
Our custom disc springs fabrication service provides durable and affordable springs that meet your specifications for automotive, medical, aerospace, electronics, food, construction, security, marine, and more industries. Fast to send your inquiry or submit your drawings to get a free quote in the shortest time.Contact us or Email [email protected] to see how our people, equipment and tooling can bring the best quality for the best price for your custom disc springs project.
-
Can a Metal Box Spring Be Cut to Size?
-
How Is Spring Steel Made
-
A Comprehensive Guide to Spring Design Principles
-
Alloy Steel Disc Springs
-
Pressure Relief Valve Spring
-
Punching Special-Shaped Spring Sheet
The Parameters Of Torsion Springs
The torsion spring is the extreme of the variant spring, from the single torsion spring to the double torsion spring special-shaped torsion spring, and even the deformation of various torsion bars, it can be formed according to the design. Therefore, it is difficult to grasp the necessary information of the torsion spring when designing:
- Free Length.
- Controlling Diameter: (A) Outer Diameter, (B) Inner Diameter, (C) Inner Diameter Of The Casing, Or (D) Outer Diameter Of The Round Rod Passing Through.
- The Wire Size “Wire Diameter”.
- Materials (Type And Grade).
- Number Of Turns: (A) Total Turns And (b) Right-Hand Or Left-Hand.
- Torsion: The Number Of Pounds Deflected To A Certain Angle.
- Maximum Deflection (Angle From Free Position).
- The Form Of The End.
Please specify: material diameter (d), outer diameter (D), torsion arm length (L), free height (Lo), and other geometric dimensions, such as guiding moments (T 1 T 2… T j ) and corresponding and Corresponding torsion angle (Ψ)
When the spring is twisted, the material is in a state of tension or shear, such as the torsion calculation mentioned, so the limit of the torsion angle is finally caused by the failure of the material, and the original state cannot be restored when the material is plastically deformed. Therefore, it boils down to the tensile strength and shear strength of the material. Of course, the Von Mises stress calculated by the fourth strength theory is the maximum strength that the material can bear. Combined with the length of the spring, the maximum allowable torsion angle can be calculated.
The Specifications Of Our Disc Springs
- Standard parts: 0.2-14mm
- Customized parts: 300 series austenitic stainless steel: 0.2-5mm
- 3Cr13 martensitic stainless steel: 0.2-10mm
- 50CrVA/60Si2Mn: 0.2- 50mm
- Standard parts: maximum outer diameter: 250mm, minimum inner diameter 4.2mm
- Customized parts: maximum outer diameter: 600mm, minimum inner diameter 4mm
Various countries generally use silicon-manganese, chrome alum, and chrome-manganese alloy steel. Special materials used in high temperature and low temperature and corrosive environments such as anti-magnetic, corrosion-resistant and heat-resistant materials, such as nickel-based alloys and beryllium copper alloys. High fatigue life: Disc springs are shot peened in the factory to create residual stress. Anti-corrosion treatment of disc springs: The standard treatment process is zinc-phosphating and oiling. If the environment in which the disc spring works requires higher corrosion resistance, the following processes can be selected: zinc-phosphating plus wax coating galvanized zinc or chrome plating Delta Tone/Delta Seal coating Dacromet coating electrochemical coating Nickel-plated size range: OD 8.0 mm-800 mm. DIN 2093 (DIN 17221, DIN 17222) standard material and special request material. Disc springs with thickness greater than 0.5 mm are shot peened to improve fatigue life.