Spring steel is a type of steel that is characterized by its ability to regain its shape after being deformed. It finds extensive use in a wide array of applications, from automotive suspensions to consumer products. Understanding how spring steel is made requires delving into the intricacies of metallurgy, exploring the processes and techniques that transform ordinary steel into a resilient material capable of enduring repeated stress and strain. This article will comprehensively explore the history, composition, properties, and the elaborate manufacturing process of spring steel.
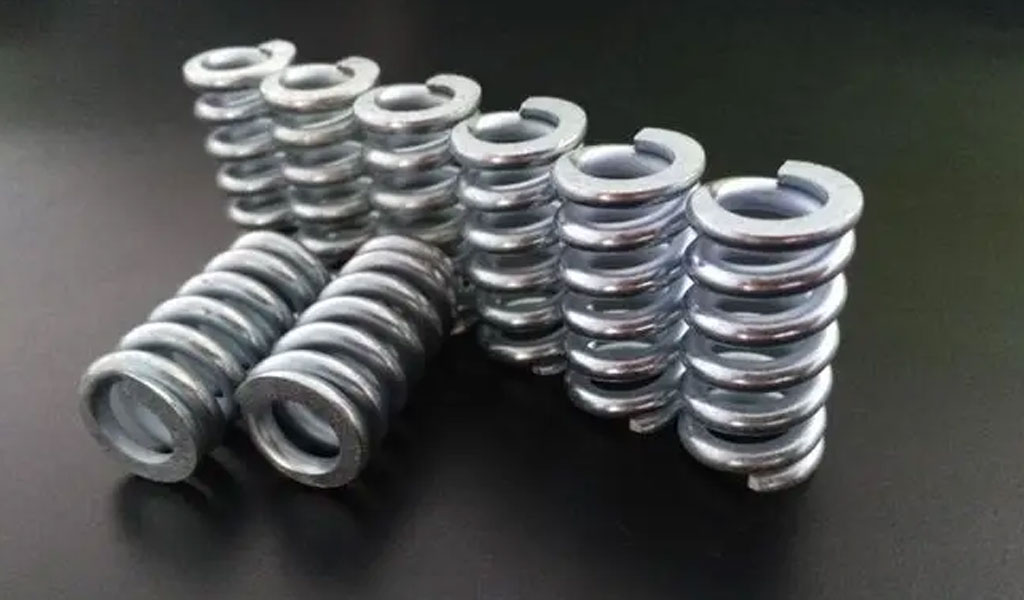
What is Spring Steel?
Spring steel, a versatile and specialized form of steel, is engineered to exhibit exceptional elasticity and resilience. It derives its name from its primary application, as it is primarily used in the manufacture of springs.
However, spring steel is not confined to springs alone; its unique properties make it a vital component in a wide array of applications. This section delves into the definition and characteristics of spring steel.
Spring Steel Definition
Spring steel is a group of high-carbon steel alloys that are specifically designed to maintain their shape and elasticity under stress. Unlike other steel alloys, spring steel can deform significantly and return to its original shape, even after experiencing substantial mechanical strain. This inherent ability to store and release mechanical energy makes spring steel invaluable in various engineering applications.
The Historical Significance of Spring Steel
The historical significance of spring steel traces its roots back to ancient civilizations. While the exact origins are difficult to pinpoint, spring steel has played a crucial role in the development of numerous technologies and industries. Understanding the historical context provides insights into the evolution of spring steel and its applications.
Early Uses
Early examples of spring steel applications can be traced back to ancient China, where it was employed in the construction of weaponry such as swords. The Chinese were among the first to discover the benefits of quenching and tempering steel to enhance its strength and resilience. Spring steel was also used in the design of torsion springs and other mechanical components.
Industrial Revolution
During the Industrial Revolution, the demand for spring steel soared as various industries, including transportation, machinery, and manufacturing, sought advanced materials for their evolving technologies. Innovations in metallurgy and steel production techniques allowed for the mass production of spring steel, further fueling the growth of these industries.
Modern Era
In the modern era, spring steel continues to be an integral part of engineering and manufacturing. Its applications have expanded to include automotive suspension systems, aerospace components, consumer electronics, and countless other products that require the unique properties of spring steel to function effectively.
Key Properties of Spring Steel
Spring steel possesses a distinctive set of properties that make it well-suited for its intended applications. These properties enable spring steel to withstand repeated loading and deformation while maintaining its integrity and performance.
Elasticity
Elasticity is one of the defining characteristics of spring steel. It refers to the material’s ability to deform under applied force and return to its original shape when the force is removed. Spring steel can endure significant elongation, bending, or twisting while recovering its initial configuration. This property is essential for springs, which rely on elasticity to store and release mechanical energy.
Strength
Spring steel exhibits high tensile strength, which is the capacity to resist breaking or deforming under tension. This property ensures that spring steel components can withstand the substantial forces they encounter during operation. Different types of spring steel may vary in their strength characteristics, allowing engineers to select the most suitable type for specific applications.
Toughness
Toughness is a measure of a material’s ability to absorb energy without breaking or fracturing. Spring steel demonstrates excellent toughness, enabling it to absorb the energy generated by dynamic loads and impacts without failing. This characteristic is crucial for applications like suspension systems and safety mechanisms.
Durability
Spring steel is highly durable, with the capacity to endure prolonged use and cyclic loading without succumbing to fatigue or wear. Its resistance to fatigue ensures that spring steel components maintain their performance and structural integrity over time, which is essential for reliable and long-lasting products.
Common Applications of Spring Steel
Spring steel finds widespread use in a multitude of industries, thanks to its unique properties. The versatility of spring steel allows it to be tailored to specific applications, and its durability and reliability make it indispensable in various engineering and manufacturing contexts.
Automotive Industry
One of the most prominent applications of spring steel is in the automotive industry. It is used to manufacture suspension springs, including coil springs and leaf springs. These springs provide the necessary support and shock absorption to ensure a smooth and stable ride.
Aerospace
In the aerospace sector, spring steel is employed in critical components such as landing gear and actuation systems. The ability to maintain performance under extreme conditions and repeated cycles is vital in aerospace applications where safety and reliability are paramount.
Consumer Electronics
Spring steel is often utilized in the design of various consumer electronics, particularly in components like battery contacts, connectors, and switches. Its electrical conductivity and elasticity are advantageous in these applications.
Firearms
Historically, spring steel has been a crucial material in the manufacturing of firearms. Springs in firearms play essential roles in actions, triggers, and magazines, and the reliability of these springs is critical for firearm safety and performance.
Industrial Machinery
Spring steel is integral to the operation of industrial machinery, where it can be found in various components such as mechanical seals, conveyor systems, and clutch assemblies. Its ability to withstand heavy loads and endure cyclic stress makes it an ideal choice in industrial settings.
Construction
In the construction industry, spring steel is utilized for safety applications, such as door locks and hinges. Its toughness and resilience are essential for ensuring the security and functionality of building components.
Medical Devices
Spring steel is also employed in the medical field for the production of surgical instruments, medical devices, and implants. Its biocompatibility and reliability are crucial for medical applications.
Consumer Products
Spring steel can be found in everyday consumer products, including zippers, scissors, and various hand tools. Its ability to maintain its shape and function under repeated use enhances the performance and longevity of these items.
Spring steel is a remarkable material with a rich history and a wide range of applications. Its unique combination of elasticity, strength, toughness, and durability makes it an invaluable component in numerous industries, contributing to the functionality and safety of products and systems that touch every aspect of our lives. The development and refinement of spring steel over the centuries have led to its ubiquity in modern engineering, and its significance is unlikely to diminish in the future as new applications continue to emerge.
The Raw Materials
The production of spring steel begins with the selection of high-quality raw materials, with iron and steel serving as the primary ingredients. These materials provide the foundation for creating a steel alloy with the desired characteristics.
Iron: The Base Metal
Iron is the fundamental raw material used in steelmaking. It is abundant in nature and forms the basic structure of all steel alloys. In the steel production process, iron ore is extracted from mines and undergoes a series of transformations to become iron or pig iron. Pig iron is the starting point for producing various types of steel, including spring steel.
Steel: The Intermediate Product
Steel is an alloy of iron and carbon, and it plays a crucial role in the manufacturing of spring steel. Steel provides the necessary structural integrity, while the addition of carbon and other alloying elements imparts the specific properties required for spring applications. The quality and composition of steel are carefully controlled to meet the stringent standards for spring steel production.
Alloying Elements
The addition of alloying elements is a critical step in the production of spring steel. These elements, carefully selected and combined in precise quantities, contribute to the unique properties of spring steel. Some of the most common alloying elements used in spring steel production include carbon, manganese, silicon, chromium, and vanadium.
Carbon
Carbon is a primary alloying element in spring steel. Its content significantly influences the steel’s hardness and strength. Higher carbon content increases hardness and tensile strength, making the steel more suitable for applications requiring rigidity and durability. However, excessive carbon content can lead to brittleness, so the amount of carbon must be carefully controlled to achieve the desired balance of properties.
Manganese
Manganese is often added to spring steel to enhance its hardenability, which refers to the ability of the steel to respond to heat treatment and achieve the desired level of hardness. It also contributes to the steel’s resistance to wear and deformation, making it a valuable alloying element in spring steel.
Silicon
Silicon is used in spring steel to improve its resistance to heat and corrosion. It also aids in deoxidizing the steel during the refining process. Silicon can enhance the steel’s ability to withstand high temperatures, which is beneficial in applications exposed to extreme heat.
Chromium
Chromium is an alloying element that can enhance the corrosion resistance of spring steel. It forms a protective oxide layer on the steel’s surface, reducing its susceptibility to rust and oxidation. This is especially important in applications where the steel is exposed to harsh environmental conditions.
Vanadium
Vanadium is added to spring steel to increase its strength and toughness. It refines the steel’s grain structure, making it more resistant to fatigue and wear. Vanadium is particularly valuable in applications where the spring steel undergoes cyclic loading and requires long-term durability.
Importance of High-Quality Raw Materials
The quality of raw materials is of paramount importance in spring steel production. High-quality iron and steel, along with precisely controlled alloying elements, are essential to achieving the desired properties and performance characteristics. Low-quality raw materials can lead to defects and inconsistencies in the final product, jeopardizing the reliability and safety of spring steel applications.
Consistency and Uniformity
High-quality raw materials ensure consistency and uniformity in the steel alloy. This is vital for maintaining the desired mechanical properties and structural integrity across all spring steel components. Inconsistent materials can lead to variations in performance and may result in premature failure.
Impact on Manufacturing Process
The quality of raw materials also affects the efficiency of the manufacturing process. Inferior materials may require additional processing steps to remove impurities, which can increase production costs and lead to longer production times. High-quality materials streamline the manufacturing process and reduce the need for extensive post-processing.
Safety and Reliability
The safety and reliability of spring steel applications are directly tied to the quality of raw materials. In critical industries such as aerospace, automotive, and medical devices, any compromise in material quality can have severe consequences. High-quality raw materials are essential for ensuring the safety and functionality of spring steel components.
Sourcing of Raw Materials
Sourcing high-quality raw materials is a crucial aspect of spring steel production. Manufacturers must establish reliable supply chains and adhere to strict quality control measures to ensure the consistent quality of their products.
Iron Ore Mining
The first step in sourcing raw materials is the extraction of iron ore from mines. Mining companies work to locate and access high-quality iron ore deposits. The selection of iron ore sources is a critical decision, as it impacts the quality of the final steel product.
Steel Production
The production of steel from iron ore involves several steps, including smelting and refining. Steel producers carefully control the composition and quality of the steel to meet the specific requirements for spring steel production. Large steel mills are often involved in this stage, and their reputation for quality is paramount.
Alloying Elements
Alloying elements, such as carbon, manganese, silicon, chromium, and vanadium, must be sourced from reliable suppliers. Manufacturers typically work with established suppliers known for producing high-purity alloying elements. The precise quantity and composition of these elements are controlled to achieve the desired spring steel properties.
Quality Control
Stringent quality control measures are implemented throughout the sourcing process. This includes testing and inspecting raw materials to ensure they meet the necessary specifications. Testing methods may include chemical analysis, mechanical testing, and metallurgical examinations.
The production of spring steel relies on a combination of high-quality iron, steel, and carefully selected alloying elements. The careful control of these raw materials and the precise composition of the steel alloy are fundamental to achieving the unique properties required for spring applications. Sourcing high-quality materials and maintaining strict quality control processes are essential to producing reliable and durable spring steel products.
The Manufacturing Process
The production of spring steel involves a complex and precise manufacturing process that transforms raw materials into a specialized steel alloy with the desired properties. This section explores the steps involved in the production of spring steel.
Melting and Refining
The initial stages of spring steel production focus on melting and refining the raw materials to create a high-quality steel alloy. Various processes are employed to achieve this.
- Blast Furnace Process : The blast furnace process is a traditional method for producing iron from iron ore. It involves heating iron ore, coke (a form of coal), and limestone in a large, vertical furnace. The resulting molten iron, known as pig iron, serves as the primary source of iron for further steel production.
- Electric Arc Furnace Process : Electric arc furnaces (EAFs) are used to melt and refine scrap steel and pig iron. This process is highly energy-efficient and allows for precise control over the composition of the steel. EAFs are essential in the recycling of steel and reducing the reliance on virgin iron ore.
- Oxygen Converter Process : The oxygen converter process, also known as the basic oxygen furnace (BOF) process, involves blowing oxygen onto the surface of molten pig iron or scrap steel. This removes impurities and refines the steel, resulting in a high-quality base material for spring steel.
Alloying and Refining
Alloying is a critical step in spring steel production, as it involves the introduction of specific alloying elements to create the desired properties.
- Introduction of Alloying Elements : Alloying elements, such as carbon, manganese, silicon, chromium, and vanadium, are added in precise quantities to the molten steel. The composition of these elements is carefully controlled to achieve the desired balance of properties, including strength, toughness, and hardness.
- Deoxidation and Desulfurization : Deoxidation and desulfurization processes are employed to remove unwanted elements from the steel. Oxygen and sulfur are common impurities that can negatively impact the steel’s quality. Deoxidation and desulfurization agents are added to the molten steel to eliminate these impurities.
Casting and Solidification
Once the steel alloy is refined and alloyed to the desired composition, it is cast into various forms, including continuous casting and ingot casting.
- Continuous Casting : Continuous casting is a modern method of forming steel into a continuous length. It involves pouring the molten steel into a water-cooled mold, which results in a solidified, continuous steel strand. This process is efficient and minimizes the need for subsequent rolling.
- Ingot Casting : Ingot casting, on the other hand, involves pouring the molten steel into molds to create large, solid blocks known as ingots. These ingots are then processed further through rolling to reduce their thickness and width.
Rolling and Hot Working
The steel undergoes hot working, primarily through the hot rolling process, to shape and refine it further.
Hot Rolling Process :
Hot rolling is a technique where the steel is heated and passed through a series of rolling mills to reduce its thickness and width. This process enhances the steel’s mechanical properties and prepares it for further processing.
- Reduction in Thickness and Width : During the hot rolling process, the steel is gradually reduced in thickness and width, resulting in a semi-finished product with the desired dimensions. This process also refines the microstructure of the steel, improving its strength and toughness.
- Annealing : Annealing is a heat treatment process that involves heating the steel to a specific temperature and then slowly cooling it. This relieves internal stresses and refines the microstructure, making the steel more ductile and ready for further processing.
- Skin Passing : Skin passing is an additional rolling process that further refines the surface finish and dimensions of the steel. It removes imperfections and ensures uniform thickness.
Cold Working and Tempering
Cold working and tempering are essential steps to achieve the desired hardness and strength in spring steel.
Spring steel is typically cold worked through processes such as cold rolling or cold drawing. This further increases its strength and refines its mechanical properties. The steel is then tempered to relieve internal stresses and enhance toughness.
Heat Treatment Processes
Heat treatment is a critical aspect of spring steel production, as it influences its hardness and resilience.
- Austenitizing : Austenitizing involves heating the steel to a specific temperature, allowing it to transform into an austenitic microstructure. This prepares the steel for subsequent quenching.
- Quenching : Quenching is the rapid cooling of the steel to create a martensitic microstructure. This results in increased hardness but can make the steel brittle, necessitating further tempering.
- Tempering : Tempering involves reheating the steel to a controlled temperature, which reduces its hardness to a desired level while maintaining toughness. Tempering is a crucial step to ensure the steel exhibits the right balance of properties for spring applications.
- Martensite Transformation : Martensite transformation is the conversion of the steel’s microstructure into a martensitic structure, which contributes to its hardness and strength.
Cold Forming and Shaping
Spring steel is often shaped using various cold forming techniques to create the specific components required for different applications.
Shaping methods may include cutting, bending, stamping, and coiling. These processes are essential for manufacturing springs, clips, and various other components that rely on the steel’s elasticity and resilience.
Surface Finishing
To ensure the steel meets the required surface finish and performance characteristics, it often undergoes additional processes.
- Grinding : Grinding is used to achieve precise dimensions and surface finish. It removes any imperfections and ensures that the steel components meet tight tolerances.
- Polishing : Polishing enhances the steel’s appearance and smoothness. It is often used in applications where aesthetics are important, such as in high-end consumer products.
- Coating : In some cases, spring steel components are coated to provide additional protection against corrosion and wear. Coatings can include zinc, nickel, or other corrosion-resistant materials.
The manufacturing process of spring steel is a multifaceted journey that transforms raw materials into a specialized alloy with the unique properties required for spring applications. The combination of melting, alloying, casting, hot working, heat treatment, and cold shaping results in a versatile material that is fundamental to various industries, from automotive and aerospace to consumer products and construction. Careful control of each stage of the process is essential to ensure the spring steel meets the strict standards for quality and performance.
Types of Spring Steel
Spring steel is not a one-size-fits-all material. Various types of spring steel exist, each tailored to specific applications and requirements. In this section, we explore the characteristics, composition, and applications of some of the most common types of spring steel.
Music Wire
Music wire is a high-carbon steel alloy known for its exceptional tensile strength and uniformity. It is often cold-drawn and tempered to achieve the desired spring properties. Music wire is recognized for its excellent elasticity, corrosion resistance, and the ability to withstand high stress and fatigue. This type of spring steel is commonly used in applications that require precision, such as musical instruments, mechanical clocks, and precision springs.
Oil-Tempered Wire
Oil-tempered wire is a type of spring steel that undergoes a specific heat treatment process using oil as the quenching medium. This process results in excellent toughness and resistance to wear and fatigue. Oil-tempered wire is characterized by its durability and ability to withstand heavy loads, making it suitable for applications like automotive suspension systems, agricultural machinery, and industrial equipment.
Stainless Steel
Stainless steel is another type of spring steel, and it is known for its resistance to corrosion and staining. While various grades of stainless steel are used for different applications, stainless spring steel is often austenitic or precipitation-hardening. It is suitable for applications where maintaining corrosion resistance is critical, such as in marine environments, chemical processing equipment, and medical devices.
Chrome Vanadium
Chrome vanadium spring steel is an alloy that incorporates both chrome and vanadium to enhance its properties. It offers excellent tensile strength, toughness, and resistance to wear and fatigue. Chrome vanadium spring steel is commonly used in automotive suspension components, hand tools, and industrial machinery.
Differences in Composition and Properties
The composition of each type of spring steel is tailored to achieve specific properties, and this results in differences in their characteristics.
- Music Wire: High-carbon content for excellent tensile strength and uniformity. Cold-drawn and tempered for precise spring properties.
- Oil-Tempered Wire: Heat-treated with oil as the quenching medium, resulting in exceptional toughness, wear resistance, and fatigue resistance.
- Stainless Steel: Various grades of stainless steel are used, with corrosion resistance being a key feature. Austenitic and precipitation-hardening stainless steels are common choices.
- Chrome Vanadium: Alloyed with chrome and vanadium for improved tensile strength, toughness, and resistance to wear and fatigue.
Applications and Suitability of Each Type
Each type of spring steel is well-suited to particular applications based on its unique properties.
- Music Wire: Ideal for precision applications where uniformity, high tensile strength, and corrosion resistance are critical. Commonly used in musical instruments, mechanical clocks, and precision springs.
- Oil-Tempered Wire: Suitable for applications where durability, toughness, and resistance to wear and fatigue are essential. Widely used in automotive suspension systems, agricultural machinery, and industrial equipment.
- Stainless Steel: Used in applications that require corrosion resistance, such as marine environments, chemical processing equipment, and medical devices. The choice of specific stainless steel grade depends on the specific requirements.
- Chrome Vanadium: Offers a balance of high tensile strength, toughness, and resistance to wear and fatigue. It is commonly used in automotive suspension components, hand tools, and industrial machinery.
The type of spring steel chosen for a particular application depends on the specific requirements of that application. Whether the focus is on precision, durability, corrosion resistance, or a combination of these properties, there is a type of spring steel that can meet those needs. Understanding the differences in composition and properties of various spring steel types is crucial for selecting the right material for a given application, ensuring the desired performance and reliability.
Quality Control and Testing
Ensuring the quality of spring steel is of paramount importance in its production, as the reliability and performance of the steel in various applications depend on its properties. This section explores the significance of quality control in spring steel production, the methods and equipment used for inspection, and the adherence to industry standards and specifications.
Importance of Quality Control in Spring Steel Production
Quality control in spring steel production is critical for several reasons:
- Reliability and Safety : Spring steel is used in numerous applications where reliability and safety are paramount, such as automotive suspension systems and aerospace components. Any defects or inconsistencies in the material can compromise the integrity of these applications, potentially leading to accidents or failures.
- Performance : The mechanical properties of spring steel, including tensile strength, elasticity, and toughness, must meet specific standards to ensure the spring functions as intended. Quality control is essential to verify that the steel’s properties align with the requirements of its intended use.
- Consistency : Uniformity in material properties is crucial. Inconsistent spring steel can result in variations in performance and lead to manufacturing issues and product failures.
- Cost Efficiency : Quality control also helps in avoiding costly post-processing or rework to correct defects in the steel. By ensuring high-quality spring steel from the start, production costs can be reduced.
Inspection Methods and Equipment
Various inspection methods and equipment are employed in quality control to assess the properties and quality of spring steel.
- Tensile Testing : Tensile testing is a common method used to evaluate the mechanical properties of spring steel. It measures the steel’s response to tensile (pulling) forces and provides data on properties such as yield strength, ultimate tensile strength, and elongation. Tensile testing machines apply a controlled force to the steel specimen until it breaks, allowing for the determination of its strength and ductility.
- Hardness Testing : Hardness testing is used to assess the steel’s resistance to permanent deformation and surface wear. The Rockwell, Brinell, and Vickers hardness tests are commonly employed. These tests involve applying a known force to an indenter, and the hardness value is determined based on the depth of indentation or the size of the impression left on the material.
- Microstructure Analysis : Microstructure analysis involves examining the internal structure of the steel at a microscopic level. It helps assess the distribution of phases, grain size, and the presence of any defects. Techniques like optical microscopy, scanning electron microscopy (SEM), and transmission electron microscopy (TEM) are used to perform microstructure analysis.
- Non-Destructive Testing : Non-destructive testing (NDT) methods are used to assess the quality of spring steel without causing any damage to the material. Common NDT techniques include ultrasonic testing, radiographic testing, magnetic particle testing, and dye penetrant testing. These methods are essential for detecting internal defects, cracks, and inclusions that may not be visible to the naked eye.
Meeting Industry Standards and Specifications
Adherence to industry standards and specifications is a fundamental aspect of quality control in spring steel production. These standards define the requirements and characteristics that spring steel must meet to be considered safe and reliable for specific applications.
- ASTM (American Society for Testing and Materials) : ASTM standards provide comprehensive guidelines for the mechanical, chemical, and physical properties of spring steel. These standards cover different types of spring steel and various testing methods to ensure compliance with industry norms.
- ISO (International Organization for Standardization) : ISO standards play a significant role in ensuring the quality of spring steel on a global scale. ISO standards address various aspects of spring steel production, including material properties, testing procedures, and acceptance criteria.
- Industry-Specific Standards : Certain industries, such as the automotive, aerospace, and medical device sectors, have their own specific standards and specifications for spring steel. Manufacturers must meet these industry-specific requirements to supply spring steel for these applications.
Quality control and testing are integral to the production of spring steel, as they ensure the material’s reliability, safety, and performance. Inspection methods such as tensile testing, hardness testing, microstructure analysis, and non-destructive testing provide valuable data on the material’s properties and quality. Adherence to industry standards and specifications is essential to meet the specific requirements of different applications and ensure the consistent quality of spring steel products. By employing stringent quality control measures and thorough testing, manufacturers can produce spring steel that meets the highest standards and serves as a trusted material in a wide range of industries.
In Conclusion
The production of spring steel is a complex and highly regulated process that involves a series of precise steps to transform raw materials into a material with unique properties. Spring steel is vital in various industries, from automotive and aerospace to consumer products and medical devices, where its exceptional elasticity, strength, toughness, and durability are crucial for reliable and safe performance.
Throughout the manufacturing process, quality control and testing play a pivotal role in ensuring that spring steel meets the rigorous standards and specifications required for its intended applications. Quality control measures, including inspection methods such as tensile testing, hardness testing, microstructure analysis, and non-destructive testing, provide valuable insights into the material’s properties and quality. These tests help identify defects, inconsistencies, and deviations from the required standards.
Moreover, adherence to industry-specific standards, such as those established by ASTM, ISO, and sector-specific regulations, is essential to guarantee that spring steel meets the stringent requirements of different applications. Compliance with these standards ensures that spring steel is not only reliable but also safe for use in critical industries where performance and safety are non-negotiable.
The selection of the right type of spring steel for a given application is equally important. Various types of spring steel, such as music wire, oil-tempered wire, stainless steel, and chrome vanadium, cater to diverse needs based on their unique properties. Choosing the appropriate type of spring steel can make the difference between a successful and reliable product and one prone to failure or malfunction.
In a world where precision and reliability are paramount, spring steel’s role in engineering, manufacturing, and everyday life cannot be overstated. Its evolution over centuries, from ancient Chinese weaponry to cutting-edge aerospace components, reflects the continual demand for materials that offer the right combination of strength and flexibility. The commitment to quality control, testing, and adherence to standards ensures that spring steel remains at the forefront of materials science and continues to contribute to innovation and progress in countless industries.