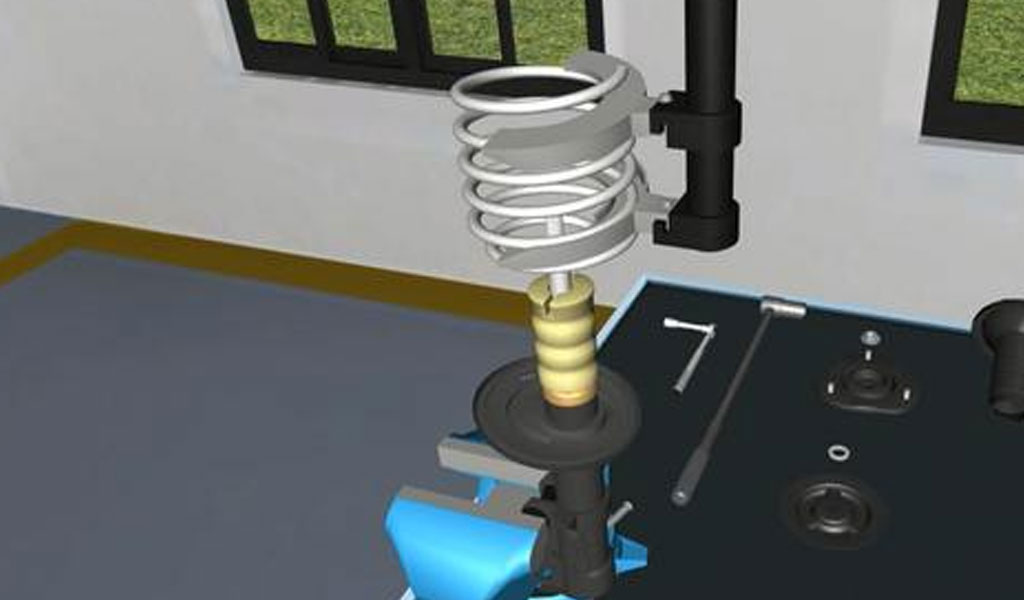
In the realm of engineering and industrial applications, the management of vibration has emerged as a critical factor in ensuring the longevity, efficiency, and safety of various systems and structures. Unwanted vibrations can lead to a range of issues, from accelerated equipment wear and reduced precision to compromised human comfort and even catastrophic failures. As a response to these challenges, engineers have turned to innovative solutions such as helical vibration isolators, a technology designed to minimize the transmission of vibrations. This article delves into the concept, design principles, applications, and advantages of helical vibration isolators, shedding light on their effectiveness in reducing vibrations and improving overall system performance.
Understanding Vibration: The Need for Isolation
Vibration is a ubiquitous phenomenon caused by the oscillation of particles or objects around their equilibrium positions. While some forms of vibration are desirable and even necessary for specific applications, many situations require effective vibration control. Uncontrolled vibrations can result from various sources, including machinery operation, ground motion, vehicle movement, and environmental factors. These vibrations can lead to mechanical fatigue, decreased accuracy, compromised structural integrity, and diminished human comfort. Consequently, mitigating vibration-related issues is paramount in diverse sectors such as manufacturing, aerospace, automotive, construction, and more.
Introducing Helical Vibration Isolators
Helical vibration isolators, also known as helical isolators or helical mounts, are advanced mechanical devices designed to attenuate or isolate vibrations by introducing damping and isolation techniques. These isolators consist of a helical spring element, which provides the primary mechanism for absorbing and dissipating vibration energy. The fundamental principle behind their operation is based on the conversion of mechanical energy into thermal energy through the controlled deformation of the helical spring.
Design Principles of Helical Vibration Isolators
The effectiveness of helical vibration isolators is deeply rooted in their engineering and design principles. These isolators are typically composed of several key components:
- Helical Spring: The heart of the isolator, the helical spring, is usually made from materials with high elasticity and damping properties. This spring element is responsible for absorbing and dissipating vibration energy.
- Mounting Hardware: The isolator is equipped with mounting hardware that enables its integration into various systems. This hardware can include threaded connectors, base plates, and attachment points.
- Housing or Casing: To protect the internal components from environmental factors and ensure durability, helical isolators often feature a housing or casing made from materials resistant to corrosion, moisture, and other detrimental agents.
- Adjustment Mechanism: Some isolators offer the ability to adjust the stiffness or damping characteristics of the spring, allowing engineers to fine-tune the isolator’s performance to specific vibration profiles.
How Helical Vibration Isolators Work
Helical vibration isolators work by intercepting the transmission path of vibration energy between the source of vibration and the target system. When vibrations are generated, the helical spring element undergoes deformation, converting the mechanical energy into thermal energy through internal friction. This process effectively dissipates the vibrational energy, preventing it from propagating further. The result is a significant reduction in the amplitude and frequency of vibrations transmitted to the supported equipment or structure.
Applications of Helical Vibration Isolators
The versatility of helical vibration isolators makes them suitable for a wide range of applications across various industries:
- Precision Manufacturing: High-precision manufacturing equipment, such as CNC machines and semiconductor fabrication tools, can be sensitive to vibrations. Helical isolators aid in maintaining the required levels of accuracy and repeatability.
- Aerospace and Defense: Sensitive instruments, avionics, and communication equipment in aerospace and defense settings benefit from vibration isolation to ensure optimal performance and reliability.
- Medical Imaging: Medical devices like MRI machines are prone to malfunction if exposed to vibrations. Helical isolators help uphold the stability needed for accurate imaging.
- Laboratories: Research facilities housing delicate experiments, electron microscopes, and vibration-sensitive setups rely on isolators to eliminate disturbances.
- HVAC Systems: Heating, ventilation, and air conditioning (HVAC) units can generate vibrations that affect indoor comfort. Helical isolators reduce such vibrations, enhancing occupant well-being.
- Construction and Architecture: Large buildings and skyscrapers can sway due to wind and seismic activity. Helical vibration isolators mitigate these vibrations, assuring occupant safety and comfort.
- Transportation: Helical isolators contribute to smoother rides in vehicles, trains, ships, and aircraft by minimizing vibrations experienced by passengers and cargo.
Advantages of Helical Vibration Isolators
Helical vibration isolators offer several distinct advantages:
- Effective Vibration Reduction: Helical isolators excel at reducing vibrations across a broad frequency range, making them suitable for diverse applications.
- Easy Installation: The modular design of helical isolators allows for straightforward integration into existing systems without extensive modifications.
- Durability: Helical isolators are constructed from robust materials that ensure long-term performance and resistance to environmental factors.
- Customizability: Some isolators allow engineers to customize their stiffness and damping characteristics to align with specific vibration profiles.
- Maintenance-Free: Helical isolators generally require minimal maintenance, contributing to their cost-effectiveness over their operational life.
Challenges and Considerations
While helical vibration isolators offer remarkable benefits, it’s important to acknowledge potential challenges and considerations:
- Frequency Range: Isolator performance can vary based on the frequency range of vibrations. Proper selection is crucial to ensure effective vibration reduction across the desired spectrum.
- Load Capacity: Helical isolators have load limits that need to be considered during design and selection to prevent overloading and potential failure.
- Resonance Effects: Improperly matched isolators can inadvertently amplify certain frequencies, leading to resonance effects that could exacerbate vibration issues.
- Environmental Conditions: Harsh environments involving extreme temperatures, corrosive substances, or high humidity might necessitate specialized isolator designs or protective measures.
Conclusion
In the dynamic world of engineering and industry, the significance of vibration control cannot be overstated. Helical vibration isolators stand as a testament to human ingenuity, offering an effective solution to the challenges posed by unwanted vibrations. By leveraging the principles of mechanical engineering, these isolators provide an avenue for enhancing stability, precision, and safety across a multitude of applications. From manufacturing to aerospace, from medical imaging to construction, the versatility of helical vibration isolators showcases their capacity to optimize performance and drive progress in various sectors. As technology continues to advance, it is likely that helical vibration isolators will play an even more pivotal role in shaping the future of vibration management, contributing to safer, more efficient, and more comfortable environments for all.