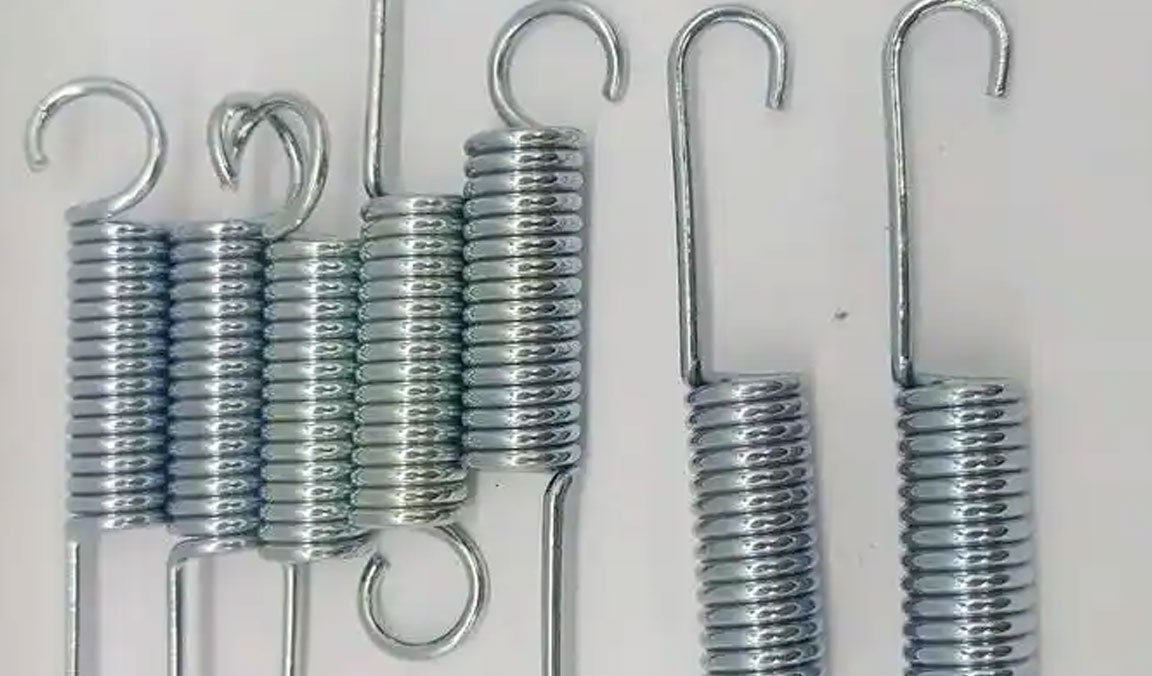
The strongest metal springs are critical components in a wide variety of industries, including aerospace, automotive, electronics, and medical devices. They serve as essential elements in mechanisms that rely on elasticity and resistance to deformation. Springs are designed to store and release mechanical energy, and their strength is directly tied to their material properties, such as tensile strength, fatigue resistance, and the ability to return to their original shape after deformation. Understanding what makes a spring “strong” involves considering factors like material composition, the geometry of the spring, and the operating conditions it will face.
Materials for Strong Metal Springs
The strongest metal springs are often made from high-strength alloys that are specifically engineered to endure high-stress conditions. These materials are selected based on their ability to withstand cyclic loading, high temperatures, and corrosion, all of which are common challenges for springs in demanding environments.
Stainless Steel
Stainless steel, particularly grades like 302, 304, 316, and 17-7 PH, is commonly used in spring applications due to its excellent combination of strength, corrosion resistance, and durability. Stainless steel springs are known for their ability to perform in harsh environments, making them ideal for aerospace, automotive, and medical applications. Among these, 17-7 PH stainless steel is often regarded as one of the strongest types of stainless steel springs due to its high tensile strength and good fatigue properties. The spring temper of stainless steel is crucial in achieving the right balance between strength and flexibility.
Alloy Steel
Alloy steels, such as 5160, 9260, and 1095, are also frequently used in the production of strong metal springs. These steels are alloyed with elements such as chromium, vanadium, molybdenum, and carbon to enhance their mechanical properties, including hardness, tensile strength, and resistance to wear. For example, 5160 steel is often used for heavy-duty applications like automotive suspension springs because of its high tensile strength and excellent fatigue resistance.
The carbon content in alloy steels is a major factor in determining their hardness. Higher carbon content results in stronger springs that are able to maintain their structural integrity under heavy loads and repeated cycles of compression or extension. However, high carbon steels tend to be more brittle, which can reduce their ability to absorb energy without failure, making the design and heat treatment processes critical for achieving optimal performance.
Music Wire
Music wire is a high-carbon steel alloy known for its exceptional tensile strength and flexibility. It is often used in the manufacture of springs that require high endurance under cyclic loading, such as those in instruments, high-performance machinery, and military applications. Music wire is typically made from a carbon steel alloy with small amounts of manganese, phosphorus, and silicon to improve its strength and spring characteristics. The wire is then drawn and heat-treated to achieve the required mechanical properties.
One of the key advantages of music wire is its high fatigue resistance, which makes it an ideal choice for applications where the spring will undergo frequent compression and expansion cycles. It is also relatively inexpensive compared to other high-strength alloys, which makes it an attractive option for cost-sensitive applications.
Titanium Alloys
Titanium alloys, such as Ti-6Al-4V, are known for their exceptional strength-to-weight ratio. Titanium springs are often used in applications where high strength is required along with the need for a lightweight design. These springs are commonly found in aerospace and medical devices, where strength and durability must be balanced with reduced weight. Titanium alloys are highly resistant to corrosion and perform well at elevated temperatures, which makes them suitable for environments where other metals might corrode or degrade.
The primary drawback of titanium springs is their cost, as titanium alloys are more expensive than other materials like stainless or alloy steels. Additionally, titanium has lower fatigue strength compared to some of the high-carbon steels used in spring manufacturing. However, for applications where weight and corrosion resistance are more critical than maximum strength, titanium springs are often the best choice.
Inconel and Nickel Alloys
Inconel, a family of high-temperature nickel-chromium alloys, is also used in the manufacture of springs that need to withstand extreme heat and stress. These alloys are characterized by their excellent performance at elevated temperatures, superior oxidation resistance, and high tensile strength. Inconel 718, for example, is widely used in turbine engines, rocket engines, and other high-performance applications that require springs to operate under extreme conditions.
The primary advantage of Inconel springs is their ability to maintain their strength and performance at temperatures exceeding those at which other metals would fail. These materials can withstand high levels of thermal stress without losing their elasticity, which is critical in applications where springs are subjected to rapid temperature fluctuations or constant high heat.
High-Speed Steel (HSS)
High-speed steel is used in manufacturing springs that need to perform under high-speed conditions or in environments where high wear resistance is required. High-speed steels, such as M2 or M42, are alloyed with tungsten, molybdenum, and cobalt to enhance their hardness, wear resistance, and resistance to softening at high temperatures. These properties make high-speed steel springs ideal for use in machinery, cutting tools, and industrial applications where they may be subjected to frequent wear and high operational speeds.
HSS springs are typically found in applications requiring both strength and toughness, as they can endure high-impact conditions without cracking or breaking. Their ability to retain hardness even at elevated temperatures also makes them suitable for use in extreme environments, though their brittleness can be a limitation in some designs.
Design Factors in Spring Strength
In addition to the material selection, the design of the spring itself is a crucial factor in determining its overall strength. A spring’s design influences how effectively it can store and release energy without experiencing permanent deformation or failure. Several design aspects must be considered to ensure the spring can handle the desired loads and cycles without failing.
Spring Geometry
The geometry of the spring, including its diameter, length, coil count, and wire thickness, plays a significant role in determining its strength. For example, the larger the diameter of the spring, the more force it can generally handle before deforming. However, increasing the diameter of the spring can also make it more difficult to compress or stretch. The number of coils is another important factor—more coils generally result in a spring that is more flexible and can handle a larger number of cycles.
Stress Distribution
Stress distribution within the spring is another important factor that affects its performance and lifespan. When a spring is compressed or stretched, the force applied to it is distributed across the entire structure. If the force is concentrated at a particular point, it can lead to localized failure. To avoid this, springs are designed to ensure uniform distribution of stress, which can be achieved through careful design and the use of advanced materials.
Surface Finish
The surface finish of the spring can also impact its strength. Rough or uneven surfaces can create stress concentrators that lead to premature failure. For high-performance applications, springs are often polished or coated to improve their surface finish and reduce the likelihood of fatigue failure. In some cases, coatings such as phosphate, chrome plating, or nitriding are applied to enhance the spring’s resistance to corrosion, wear, and fatigue.
Testing and Performance Evaluation
To ensure that springs meet the required strength criteria, they must undergo rigorous testing. The most common tests for spring strength include tensile tests, compression tests, and fatigue tests. Tensile tests measure the maximum load a spring can withstand before breaking, while compression tests determine the spring’s ability to maintain its shape and elasticity under compressive forces. Fatigue tests evaluate how well a spring can endure repeated loading cycles without failing.
Springs may also be tested under specific operating conditions to ensure they will perform effectively in their intended applications. For example, springs designed for high-temperature environments may undergo tests in ovens or furnaces to simulate real-world conditions, while springs used in medical devices may undergo biocompatibility tests to ensure they do not cause adverse reactions in the body.
Conclusion
The strongest metal springs are those that combine high tensile strength, fatigue resistance, and the ability to perform under a wide range of environmental conditions. Materials such as stainless steel, alloy steel, music wire, titanium alloys, Inconel, and high-speed steel offer a diverse array of options for designing springs that meet specific strength and performance requirements. The choice of material, along with the spring’s geometry and surface finish, determines how well the spring can withstand stress, endure repeated cycles, and retain its shape over time. By carefully selecting the right material and design, engineers can create springs that are not only strong but also reliable and durable in even the most demanding applications.