Springs are essential mechanical components that store and release mechanical energy. They are widely used in various industries and applications, from simple coil springs in pens to complex automotive suspension systems. The design of springs is a critical aspect of engineering, as it directly affects their performance, longevity, and reliability. In this comprehensive guide, we will explore the fundamental principles of spring design, covering everything from the basics of spring theory to advanced design considerations. By the end of this article, you will have a deep understanding of spring design, enabling you to create effective and efficient springs for your specific applications.
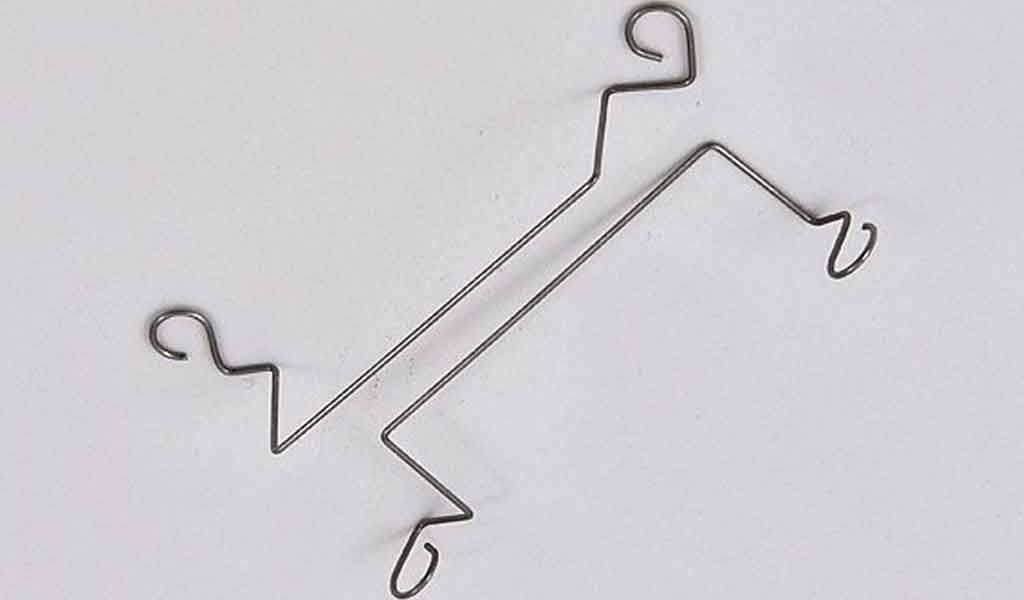
What Is Metal Springs
Springs are mechanical components that store and release energy through deformation. They come in various shapes and sizes, each designed to serve specific purposes.
The key to a successful spring design lies in understanding the underlying principles, selecting the appropriate materials, and performing precise calculations.
2. Types of Springs
Springs are categorized into several types based on their design and function:
a. Compression Springs
Compression springs are perhaps the most common type. They are designed to absorb and store energy when subjected to a compressive load. When the load is removed, the spring expands, releasing the stored energy. These springs are widely used in automotive suspension systems, door locks, and more.
b. Extension Springs
Extension springs, as the name suggests, elongate when subjected to a tensile load. They store energy when stretched and release it when the load is reduced. Extension springs are frequently found in garage doors, trampolines, and various industrial applications.
c. Torsion Springs
Torsion springs work by twisting around an axis when torque is applied. They are commonly used in applications where rotational force needs to be applied, such as in the case of clothespins, mouse traps, and many more.
d. Tension Springs
Tension springs are designed to operate under tension, often with a hook or loop at each end. They find their use in applications like retractable cords, window blinds, and garage door mechanisms.
Key Design Considerations
When designing springs, engineers must carefully consider several crucial factors to ensure the spring performs its intended function effectively. Here are four key design considerations:
Load and Deflection
Load and deflection are fundamental parameters in spring design.
Load: This refers to the force applied to the spring, whether it’s compression, tension, or torsion. Understanding the expected load is essential for selecting the appropriate spring type and material. The spring must be able to withstand the maximum load without permanent deformation or failure.
Deflection: Deflection represents how much the spring can be compressed, extended, or twisted while staying within its elastic limits. The spring’s deflection should align with the application’s requirements, allowing it to absorb or release energy as needed.
To ensure proper performance, engineers should calculate the spring rate, which is a measure of stiffness. Hooke’s Law, F = -kx, is used to determine the relationship between load (F), spring constant (k), and deflection (x).
Stress and Fatigue
Understanding the stress and fatigue characteristics of the spring material is crucial for designing a reliable and long-lasting spring.
Stress: Stress refers to the internal resistance within the spring material due to the applied load. To prevent permanent deformation or failure, it’s essential to calculate the maximum stress the spring can withstand. This involves considering factors like the spring’s cross-sectional area, material properties, and the load applied.
Fatigue: Springs are subjected to cyclic loading, which can lead to fatigue failure over time. Engineers must analyze the material’s fatigue strength and determine the number of cycles the spring can endure without failing. This information is critical for predicting the spring’s operational lifespan.
Manufacturing Tolerances
Manufacturing processes introduce variations or tolerances that can affect the spring’s performance. These tolerances must be taken into account during the design phase.
Tolerances can impact the spring’s dimensions, such as coil diameter, pitch, and wire diameter. Additionally, surface finish, straightness, and squareness of the ends can vary due to manufacturing processes.
Engineers should specify allowable tolerances in the design to ensure that the manufactured springs meet the required specifications. Understanding manufacturing limitations and selecting a reputable supplier are essential to maintain consistency in spring production.
End Configurations
The end configurations of a spring are the way it is connected to the surrounding components. Properly chosen end configurations can significantly affect a spring’s performance.
End configurations vary and can include:
- Closed and Ground Ends: These configurations provide a flat surface for load application and improve the spring’s alignment.
- Open Ends: Open ends are not ground or closed. They are less expensive to manufacture but may have some roughness at the ends.
- Squared Ends: Squared ends are perpendicular to the spring axis, providing stability when installed.
- Hooked Ends: Hooks or loops at the ends allow for easy attachment to other components.
The selection of the most suitable end configuration depends on the specific application and how the spring will be connected to other elements in the system.
Understanding load and deflection, stress and fatigue, manufacturing tolerances, and end configurations are fundamental to successful spring design. These considerations help ensure that the spring will meet the performance and durability requirements of the intended application. Properly designed and manufactured springs are crucial components in numerous mechanical systems, contributing to their reliability and functionality.
Mathematical Calculations
In spring design, several mathematical calculations are used to understand and predict the behavior of springs. These calculations are essential for determining the spring’s suitability for a specific application. Here are some of the key calculations involved:
Hooke’s Law
Hooke’s Law is a fundamental principle in spring design. It describes the linear relationship between the force applied to a spring and its resulting deformation (displacement). Mathematically, Hooke’s Law can be expressed as:
F = -kx
Where:
- F is the force applied to the spring (in Newtons, N).
- k is the spring constant or stiffness (in Newtons per meter, N/m).
- x is the displacement or deformation of the spring from its equilibrium position (in meters, m).
Hooke’s Law implies that the force required to deform a spring is directly proportional to the displacement from its rest position. The negative sign indicates that the force is applied in the opposite direction of the displacement.
Spring Rate
The spring rate, also known as the spring constant or stiffness, represents the relationship between the applied force and the resulting deflection. It is a crucial parameter in spring design and can be calculated using Hooke’s Law. The formula for spring rate is:
k = F / x
Where:
- k is the spring rate (in N/m).
- F is the force applied to the spring (in N).
- x is the resulting deflection or displacement (in m).
The spring rate defines how much force is needed to produce a specific amount of deformation in the spring. A higher spring rate means the spring is stiffer and requires more force to achieve a given deflection.
Stress and Deflection Calculations
To ensure that a spring operates within its elastic limits and can return to its original shape after deformation, engineers must perform stress and deflection calculations. These calculations help assess whether the spring material can withstand the applied load and deflection.
Stress Calculation: Stress is calculated by dividing the applied force (F) by the cross-sectional area (A) of the spring material. The formula for stress is:
σ = F / A
Where:
- σ is the stress (in Pascals, Pa or N/m²).
- F is the applied force (in N).
- A is the cross-sectional area of the spring material (in m²).
It’s essential to ensure that the calculated stress remains within the elastic limits of the chosen spring material to avoid permanent deformation or failure.
Deflection Calculation: Deflection is the change in length or displacement of the spring from its initial position due to the applied load. The deflection of a spring can be calculated using the spring rate (k) and the applied force (F). The formula for deflection is:
x = F / k
Where:
- x is the deflection (in meters, m).
- F is the applied force (in N).
- k is the spring rate or stiffness (in N/m).
This calculation helps ensure that the spring’s deflection aligns with the application’s requirements.
Mathematical calculations in spring design, including Hooke’s Law, Spring Rate, Stress, and Deflection, are vital for understanding and predicting the behavior of springs. These calculations enable engineers to design and select the right springs for specific applications, ensuring they meet performance and safety requirements. Properly designed springs provide the desired elasticity and reliability in various mechanical systems.
Manufacturing Processes
Coiling
Coiling is the primary process in spring manufacturing. It involves winding a wire or material into a specific spring shape. The key aspects of coiling include:
- Wire Selection: The choice of material and wire diameter is crucial. Different materials, such as high carbon steel, stainless steel, or specialty alloys, offer varying properties like strength, corrosion resistance, and temperature tolerance. The wire diameter influences the spring’s load-carrying capacity and stiffness.
- Pitch and Diameter: Coiling machines are set to control the pitch (distance between consecutive coils) and diameter (size of the coils) of the spring. These parameters are designed to meet the spring’s requirements for load and deflection.
- Number of Coils: The number of coils affects the spring’s overall length and can impact its flexibility and stiffness. Adjusting the number of coils can achieve specific deflection and load characteristics.
- Direction of Coiling: Springs can be wound in either a clockwise or counterclockwise direction. The direction of coiling affects the spring’s behavior, such as whether it winds tighter or looser under load.
Heat Treatment
Heat treatment is a crucial step in spring manufacturing to optimize the mechanical properties of the spring material. The heat treatment process involves heating the spring to a specific temperature and then cooling it rapidly to achieve the desired material characteristics. Key aspects of heat treatment include:
- Annealing: Annealing involves heating the spring material to a specific temperature and then slowly cooling it. This process relieves internal stresses, improves ductility, and enhances the material’s ability to deform without breaking. It also softens the material, making it easier to form during coiling.
- Quenching: After annealing, the spring material is quenched by rapidly cooling it in water or oil. This step locks in the desired mechanical properties, such as hardness and strength. Quenching can significantly affect the spring’s ability to resist deformation and fatigue.
- Tempering: Tempering involves reheating the spring material to a lower temperature to achieve the desired balance of hardness and toughness. The tempering temperature and duration are critical to ensuring that the spring material can withstand cyclic loading without breaking or deforming.
The heat treatment process is essential for fine-tuning the material properties to meet the specific requirements of the spring, such as load capacity, resistance to fatigue, and resistance to permanent deformation.
Surface Finish
The surface finish of a spring plays a role in its overall performance and longevity. Proper surface treatment can prevent corrosion, reduce friction, and improve the spring’s appearance. Key aspects of surface finish include:
- Shot Peening: Shot peening involves bombarding the spring’s surface with small metal or ceramic particles. This process induces compressive stresses in the surface, improving the spring’s resistance to fatigue and stress corrosion.
- Plating: Plating the spring with materials like zinc, nickel, or chrome can provide corrosion resistance and enhance the spring’s appearance. Plating can also reduce friction, which is important in applications where the spring must slide or rotate.
- Passivation: Passivation is a chemical process used to remove surface contaminants and enhance the corrosion resistance of stainless steel springs. It involves immersing the spring in a solution that removes free iron and other impurities from the surface.
- Painting and Coating: In some applications, springs are painted or coated with protective materials to prevent corrosion and provide a clean, aesthetically pleasing appearance.
Coiling, heat treatment, and surface finish are integral manufacturing processes in spring production. Properly executed manufacturing processes are crucial for producing high-quality springs that meet their intended specifications and perform reliably in various mechanical systems. The selection of the appropriate manufacturing methods and treatments is essential to ensure the longevity and functionality of springs in their respective applications.
In Conclusion
Metal spring design is a multifaceted and crucial aspect of mechanical engineering that underpins the functionality and reliability of countless mechanical systems. From the compression springs in your car’s suspension to the extension springs in garage doors and the torsion springs in everyday items like clothespins, springs play a pivotal role in a wide range of applications.
This comprehensive guide has provided an in-depth exploration of spring design, covering various aspects from the types of springs to the materials used, key design considerations, and the mathematical calculations involved. We have also delved into the essential manufacturing processes, including coiling, heat treatment, and surface finish.
Understanding the fundamental principles of spring design is essential for selecting the right type of spring, the appropriate material, and making accurate calculations to meet the specific requirements of a given application. Whether it’s ensuring that a spring can withstand a particular load and deflection or that it has the necessary stress and fatigue resistance, proper design considerations are vital.
Moreover, the manufacturing processes, such as coiling, heat treatment, and surface finish, are pivotal in shaping the mechanical properties of the spring material and ensuring that the spring can perform reliably over time. These processes enable the optimization of spring stiffness, strength, and corrosion resistance, among other factors.
Spring design is a dynamic field that continues to evolve, with advancements in materials and manufacturing techniques driving the development of innovative solutions for a wide array of industries, from automotive and aerospace to consumer products and medical devices.
In practice, well-designed and well-manufactured springs provide elasticity, controlled movement, and stability to mechanical systems, enhancing their overall performance and longevity. As technology advances and new materials and manufacturing methods emerge, the field of spring design will continue to adapt and grow, offering engineers and designers a rich toolbox of options to meet the ever-evolving demands of modern engineering.
In conclusion, spring design is a fundamental yet intricate discipline that bridges the gap between theory and real-world applications, contributing to the efficient and reliable operation of a vast array of mechanical systems.